Liste des articles mars - avril 2025

Show more
Abstract
The rapid growth of wearable technology demands sustainable, flexible, and lightweight energy sources for various applications, ranging from health monitoring to electronic textiles. Although wearable devices based on the piezoelectric effect are widespread, achieving simultaneous breathability, waterproofness, and enhanced piezoelectric performance remains challenging. Herein, this study aims to develop a piezoelectric nanogenerator (PENG) using ZnO nanofillers in two morphologies (nanoparticles and nanorods) with a carbon coating (ZnO@C) core–shell structure to enhance piezoelectric performance. The electrospinning technique was employed to fabricate a lightweight, breathable, and water-resistant ZnO@C/PVDF membrane, enabling in situ electrical poling and mechanical stretching to enhance electroactive β-phase formation and thus improve piezoelectric performance. A maximum power density of 384.8 μW/cm3 was obtained at RL = 104 kΩ, with a maximum Vout = 19.9 V for ZnO@C nanorod-incorporated PVDF samples. The results demonstrate that ZnO@C nanorods exhibit superior voltage output due to their larger surface-to-volume ratio, leading to enhanced interaction with PVDF chains compared to nanoparticles. The fabricated membrane showed promising results with a water vapor transmission rate (WVTR) of ∼0.5 kg/m2/day, indicating excellent breathability, and a water contact angle of ∼116°, demonstrating significant waterproofness. These findings highlight the potential of the ZnO@C/PVDF electrospun membrane as an effective piezoelectric nanogenerator and energy harvester for wearable applications.
Bagla, K. Hembram, F. Rault, F. Salaün, S. Sundarrajan, S. Ramakrishna and S. Mitra (2025). ZnO@C/PVDF Electrospun Membrane as a Piezoelectric Nanogenerator for Wearable Applications. Journal of Physical Chemistry C 129 (12): 5808-5820. https://doi: 10.1021/acs.jpcc.4c07913.
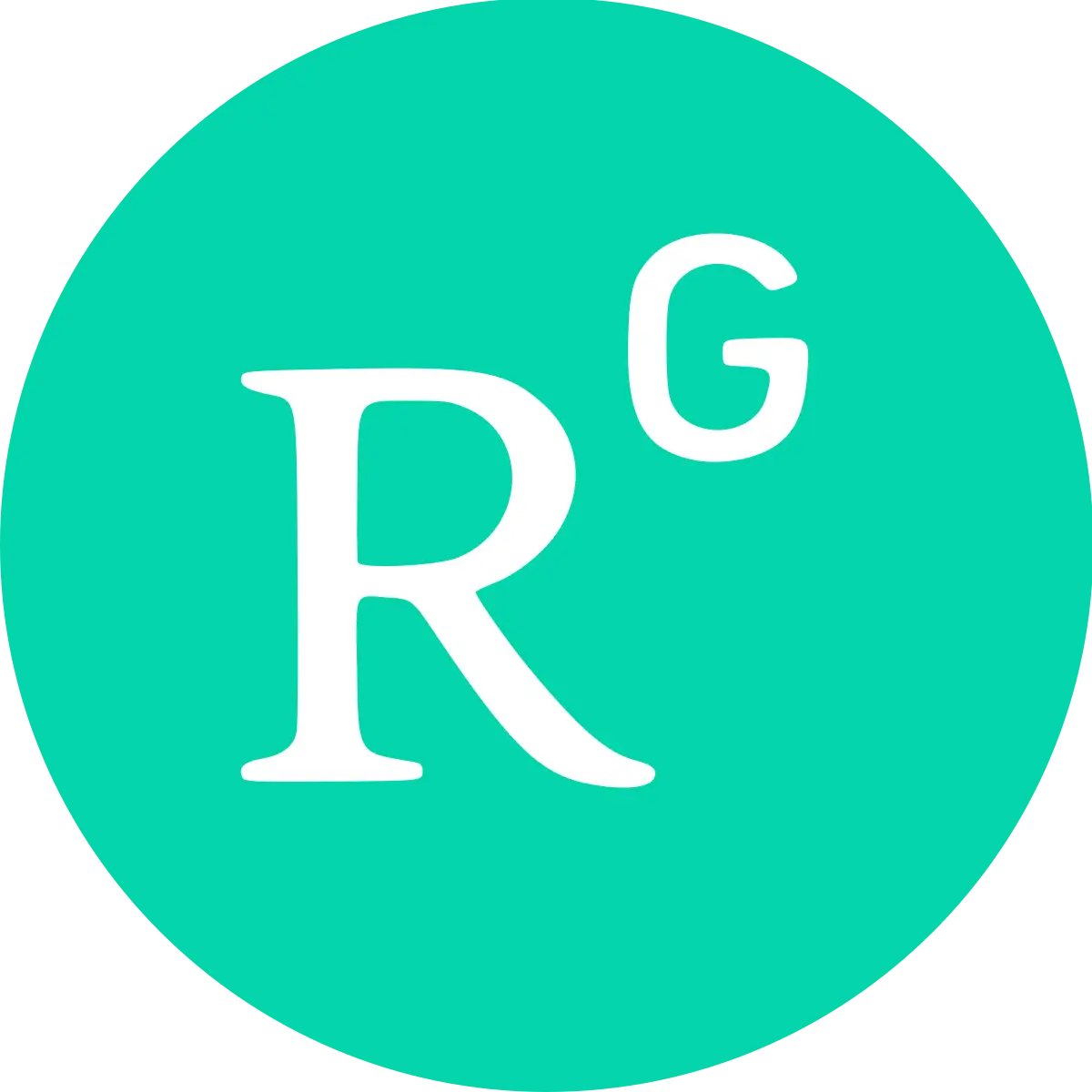
Investigation into the dynamic change mechanism of comfort perception in tight-fitting sportswear during physical activity
Pengpeng Cheng, Xianyi Zeng
Show more
Pengpeng Cheng, School of Fashion Design & Engineering, Zhejiang Sci-Tech University, Hangzhou, China
Abstract
The purpose of this study is to explore the dynamic change mechanism of clothing comfort perception during exercise, and deeply analyze the evolution characteristics of comfort perception of various body parts in different stages of exercise (warm-up, during exercise and relax after exercise). Through the test of 25 kinds of tight-fitting sportswear combinations. It is found that the influence of different clothing combinations on comfort perception presents regional differences, and the comfort change of the upper body is mainly reflected in the wet feeling and the hot feeling, while the lower body shows obvious sense of restraint; the wearing comfort of T2P1, T2P4, T3P5 and T4P3 are better than other combinations; with the extension of exercise time, the correlation of comfort of each part is gradually enhanced; the back, waist, chest and other body parts experience varying degrees of discomfort at rest, after exercise and during exercise; during exercise, the sense of restraint and stickiness of waist, hip, thigh and shank is particularly obvious. The research results fill the lack of research on the dynamic change of sportswear comfort, provide valuable design insights and promote the innovation of sportswear industry in terms of functionality and comfort. Through the in-depth analysis of the comfort change mechanism, this study provides theoretical support for the future development of sports medicine, sports psychology and smart sportswear, and helps the development of healthy sports and smart sportswear.
Cheng and X. Zeng (2025). Investigation into the dynamic change mechanism of comfort perception in tight-fitting sportswear during physical activity. Journal of Industrial Textiles 55. doi:10.1177/15280837251321856.
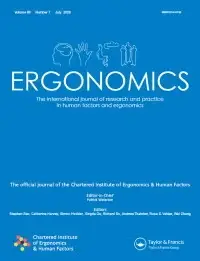
Research status and application scenarios of 3D human body modelling methods in the garment ergonomics: a systematic review
Chi, J. Xue, X. Zeng, X. Jiang and W. Zhou (2025).
Show more
Abstract
This research aims to enhance the comprehension of 3D human modelling methodologies pertinent to the garment ergonomics field. Through a search and analysis of 442 literatures, this study found that, despite the utilisation of high-resolution scanning and sophisticated 3D software, generating the vast diversity of human physiques in models remains a formidable challenge, attributed to issues such as data discrepancies and loss of detail from self-occlusion. Furthermore, through an exhaustive literature survey, this research formulates a framework for juxtaposing various modelling methodologies, analysing their technical tenets, benefits, and limitations from a synergetic and iterative standpoint. Finally, the article underscores future research trajectories, emphasising the critical need to ameliorate model precision and operational efficiency, alongside the integration of garment ergonomics knowledge into 3D human modelling. This research furnishes valuable insights and directions for forthcoming studies, aiming to drive the progression of garment ergonomics towards a more genuine and efficient.
Chi, J. Xue, X. Zeng, X. Jiang and W. Zhou (2025). Research status and application scenarios of 3D human body modelling methods in the garment ergonomics: a systematic review. Ergonomics: 1-22. doi: 10.1080/00140139.2025.2459877
Show more
a University of Lille, Ensait, Gemtex, Roubaix F59056, France
b University of Haute-Alsace, Ensisa, LPMT, Mulhouse F-68093, France
c University of Strasbourg, France
Abstract
Forming of continuous fiber-reinforced textile preforms is a commonly used technique to achieve complex shapes for light-weight composite structures. However, forming defects can reduce the quality and service life of the final product. Currently, slitting technology can be employed to produce textile composite reinforcements. This study systematically evaluates the formability of slit preforms during hemispherical forming, focusing on forming defects and the alignment of slitting locations. Advanced measurement techniques assess the influence of slitting on shear angles and wrinkle formation, providing a detailed analysis of material behavior. The experimental results indicate that precision slitting enhances preform formability by reducing shear angles and minimizing wrinkles. Moreover, slitting in the shear angle zone reduces the forming defects by decreasing the stress and forces, further diminishing shear angles and the severity of wrinkles. These findings offer critical insights into enhancing the manufacturing efficiency and quality of continuous fiber-reinforced textile composites, providing valuable guidance for future research and industrial applications.
Hu, X. Legrand and P. Wang (2025). Optimizing continuous fiber-reinforced textile preforms forming: Minimizing wrinkling through precision slitting. Thin-Walled Structures 210.
WTTPS://doi: 10.1016/j.tws.2025.113052.
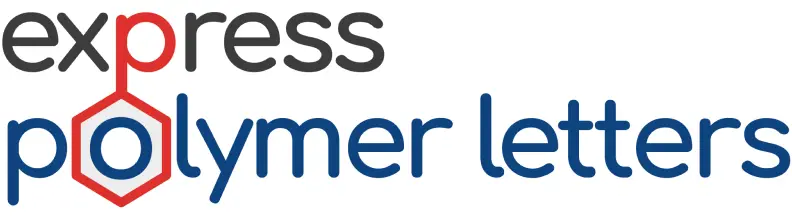
Show more
Abstract
In this work, a PDMS spinning technique is developed and enables the continuous production of a filament with a circular cross-section (~500 μm diameter). The production of continuous silicone polymer filaments can be useful in the textile field to provide new properties in applications such as weaving, knitting or composite reinforcement. The method involves injecting the pre-polymer and curing agent mixture into a heated oil bath (202–215 °C) to simultaneously shape and cure the PDMS. The morphological and mechanical properties of the filament are studied regarding the production parameters (formulation, needle diameter, bath temperature, conveyor belt speed). The most homogeneous filament is produced at the highest temperature (215°C) and conveyor belt speed (13.6 m∙min–1). When subjected to cyclic mechanical stress, the PDMS filament produced exhibits stable mechanical behavior, making it suitable for a wide range of applications.
Watel, A. Cayla, F. Salaün and F. Boussu (2025). Continuous polydimethylsiloxane filament fabrication and characterizations. Express Polymer Letters 19 (5): 494-503. https://doi: 10.3144/expresspolymlett.2025.36.
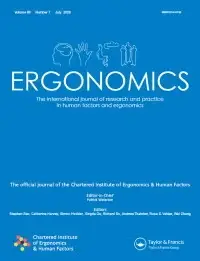
Show more
Abstract
C. Chi, X. Zeng, P. Bruniaux and G. Tartare (2025). An intelligent recommendation system for personalised parametric garment patterns by integrating designer’s knowledge and 3D body measurements. Ergonomics 68 (3): 317-337. doi: 10.1080/00140139.2024.2332772
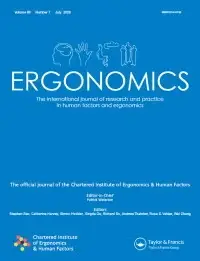
Show more
Abstract
C. Chi, X. Zeng, P. Bruniaux and G. Tartare (2025). An intelligent recommendation system for personalised parametric garment patterns by integrating designer’s knowledge and 3D body measurements. Ergonomics 68 (3): 317-337. doi: 10.1080/00140139.2024.2332772
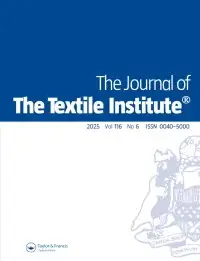
Show more
Abstract
A. Bagla, P. Goyel, F. Rault, F. Salaün and S. Mitra (2025). A breathable piezoelectric poly(vinylidene fluoride) electrospun nanofiber membrane obtained through controlling solution parameters. The Journal of The Textile Institute: 1-13. doi: 10.1080/00405000.2025.2501359